Since the demise of Endurance, you are probably aware of a number of engineering solutions for the various issues facing the E3120 turbines. We have been doing extensive due diligence on all solutions available in the market and share our thoughts with you below.
The major solutions and issues are as follows:
Parts Supply
Since the demise of Endurance, Natural Generation together with 2 other dealers, purchased all the E-series stock from the administrator and in turn engaged a specialist wind turbine parts supplier (Renewable Parts Limited) to stock and supply all existing parts.
The lead time, availability and pricing of spare parts continues to improve and Natural Generation in addition to the two companies continue to grow their own stock of spare parts and are now currently holding over £500,000 of parts.
Bedframe
There have been a number of incidents of bed plate cracks, a few of which have resulted in bed plate failure. The original Endurance solution has been prone to crack due to a weakness around certain welds.
Parts Supply
Since the demise of Endurance, Natural Generation together with 2 other dealers, purchased all the E-series stock from the administrator and in turn engaged a specialist wind turbine parts supplier (Renewable Parts Limited) to stock and supply all existing parts.
The lead time, availability and pricing of spare parts continues to improve and Natural Generation in addition to the two companies continue to grow their own stock of spare parts and are now currently holding over £500,000 of parts.
Bedframe
There have been a number of incidents of bed plate cracks, a few of which have resulted in bed plate failure. The original Endurance solution has been prone to crack due to a weakness around certain welds.
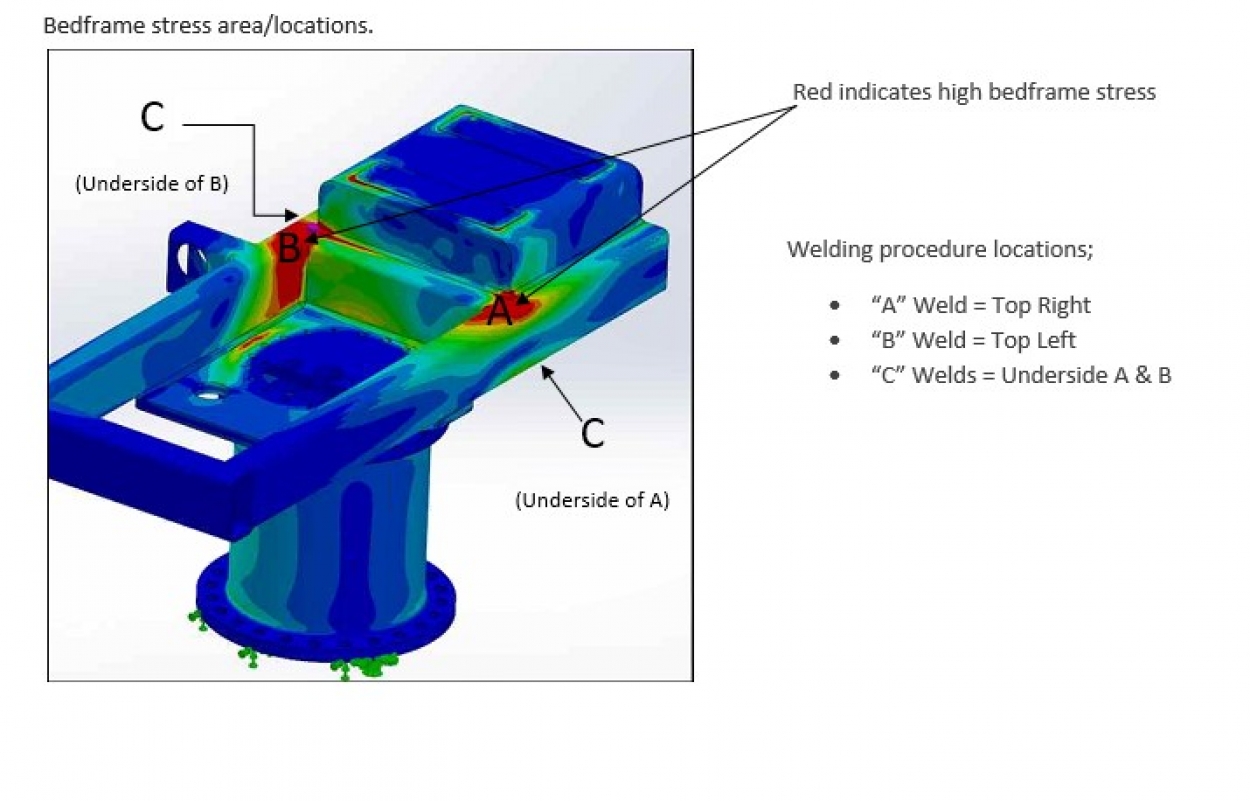
In the rare instance of bed plate failure, we are pleased to be working with Galeforce Designs. Galeforce Designs have engineered an innovative new Bedplate design, which has been accelerated fatigue tested with an applied load scenario represented over 20 years of stress on the test unit . The depth of research and testing that has gone into producing this product makes Galeforce our chosen supplier.
• Bedframe swop and process
As your chosen O&M provider we will estimate works and act as principle contractor to the project. Contract a crane lift to take the blades off, prep and then remove the nacelle. We will then place on a shipping frame and ship back to our Natural Generation purpose built workshop. During the bedframe swop process, we will supply a strip down report for components that we recommend are changed or upgraded as this is far more cost effective on the ground and can save many thousands of pounds.
Blade Repairs
We have seen a high incidence of blade failure. In conjunction with a leading engineering firm and GRP specialist we have developed a refurbishment program. This refurbishment is considerable less expensive than replacement blades, and the solution allows for any future damage to be repaired on site. To date we have installed refurbished blades on 24 of our customers turbines.
We have seen a high incidence of blade failure. In conjunction with a leading engineering firm and GRP specialist we have developed a refurbishment program. This refurbishment is considerable less expensive than replacement blades, and the solution allows for any future damage to be repaired on site. To date we have installed refurbished blades on 24 of our customers turbines.
Shafts
There have been a number of shaft failures. Our service protocol checks for any shaft degradation to avoid outright failure. As with the new bedplate design a new solution is being offered by Galeforce Designs which we are also evaluating.
There have been a number of shaft failures. Our service protocol checks for any shaft degradation to avoid outright failure. As with the new bedplate design a new solution is being offered by Galeforce Designs which we are also evaluating.
We are always working hard to identify the best and most economical solutions for your turbine.